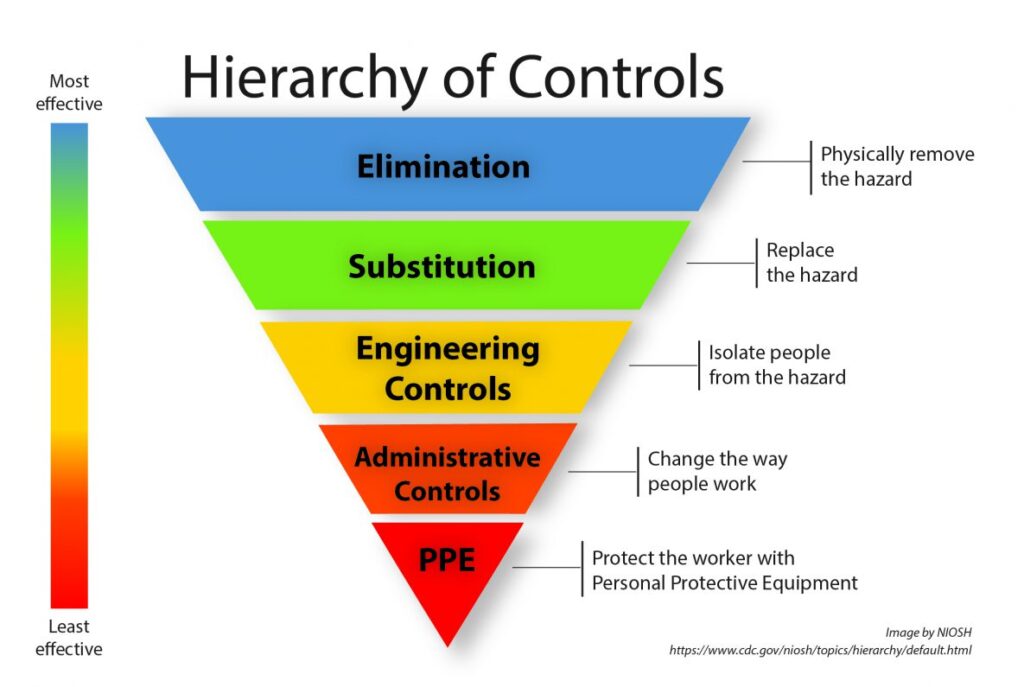
The hierarchy of hazard control is a well-known framework for setting priorities and carrying out mitigation strategies for workplace risks in occupational health and safety. This hierarchy, which has multiple levels, represents various approaches to hazard control aimed at reducing hazards and averting diseases and injuries at work. The hierarchy usually has the most effective controls at the top and the least effective controls at the bottom, arranged in descending order of effectiveness. The hazard control hierarchy is broken down as follows:
ELIMINATION:
Elimination, or totally removing the risk from the workplace, is at the top of the hierarchy. The reason this strategy works best is that it completely removes the danger. Examples include changing a dangerous material for one that is less dangerous, automating procedures to cut down on manual work in dangerous locations, or redesigning tools or procedures to completely remove the risk.
SUBSTITUTION:
Substitution is the process of replacing a hazardous item with one that poses less of a risk if eliminating it is not practical. This could mean switching to safer materials or chemicals, implementing safer procedures or equipment, or replacing risky operations with less dangerous ones. Substitution can nonetheless greatly lower the risk of injury to employees, even though it is less effective than eradication.
ENGINEERING CONTROLS:
Engineering controls entail making changes to the workspace or machinery to keep employees safe or minimize their exposure to risks. Examples include putting in ventilation systems to manage airborne contaminants, enclosing loud equipment, installing machine guards, and creating ergonomic workplaces to lower the risk of musculoskeletal injuries. Because engineering controls don’t depend on employee behavior to function, they are successful.
ADMINISTRATIVE CONTROLS:
The goal of administrative controls is to reduce exposure to hazards by altering work habits and procedures. This could entail putting safety policies and procedures into action, creating work schedules that minimize exposure to risks, educating and training employees, and using monitoring and supervision to enforce safe work practices. Administrative controls are necessary, but because they depend on compliance and human behavior, they are not as effective as engineering controls.
PERSONAL PROTECTIVE EQUIPMENTS (PPE):
PPE is your last layer of protection against risks at work. This covers tools including goggles, respirators, helmets, gloves, and protective clothes made to shield workers from particular risks. PPE is regarded as the least effective control measure since it depends on appropriate selection, proper use, and constant maintenance by the worker; yet, it is important when other controls are not possible or cannot be implemented.
It is imperative to acknowledge that the hierarchy of hazard control is not invariably linear, and that in order to effectively minimize hazards, various control measures may need to be performed either concurrently or in combination. Furthermore, it’s critical to regularly analyze and reevaluate controls to guarantee their continued efficacy and flexibility in response to shifting work environments. By adhering to this hierarchy and giving priority to controls at the top whenever it is possible, companies can systematically lower workplace risks and give their workers safer working environments.