Safety Talk: Cement Safety in the Workplace
Cement is a crucial material in the construction industry. Its versatility makes it indispensable for building foundations, roads, bridges, and countless other structures. However, working with cement poses several health and safety risks that can lead to severe injuries or long-term illnesses if not handled properly. This blog explores the hazards of cement, safety tips, and preventative measures to ensure a safe working environment. Let’s break it down in detail to create a safer workplace for everyone involved.
Understanding Cement and Its Hazards
Cement is a fine powder that, when mixed with water, forms a paste that hardens over time. While its strength and durability make it a favorite among construction workers, cement is also classified as a hazardous material due to its chemical composition. Common components include lime, silica, and other additives, which pose risks to health and safety.
Key Hazards of Cement Exposure
- Skin Irritation and Burns
Cement is highly alkaline and abrasive, which can cause skin irritation, rashes, and severe burns on contact. Wet cement is particularly hazardous because it generates heat during the curing process, intensifying its potential for harm. - Respiratory Issues
Cement dust, when inhaled, can irritate the respiratory tract. Prolonged exposure may lead to more severe conditions, such as chronic bronchitis or even silicosis, a lung disease caused by inhaling crystalline silica. - Eye Injuries
Cement particles can easily get into the eyes, leading to irritation, redness, and in severe cases, chemical burns or vision loss. - Musculoskeletal Strain
Handling heavy bags of cement often results in back injuries and musculoskeletal disorders if proper lifting techniques are not used. - Allergic Reactions
Some workers develop allergic reactions to certain components in cement, such as chromium, leading to dermatitis or other skin conditions.
Safety Precautions When Working with Cement
1. Personal Protective Equipment (PPE)
The right PPE is the first line of defense when working with cement. Employers must ensure that all workers have access to:
- Gloves: Use nitrile or neoprene gloves resistant to alkaline materials.
- Safety goggles: Protect your eyes from cement splashes and dust.
- Respirators or dust masks: Prevent inhalation of harmful cement dust.
- Coveralls and boots: Wear long-sleeved clothing and waterproof boots to shield the skin.
2. Proper Handling and Storage
- Lifting: Always use proper lifting techniques to avoid back strain. Bend your knees, keep your back straight, and lift with your legs.
- Storage: Store cement bags in a dry, ventilated area to prevent moisture exposure, which can lead to clumping and increased dust.
3. Minimize Dust Exposure
- Mix cement in well-ventilated areas or use dust control measures like wet cutting or mixing.
- Regularly clean work areas to prevent the buildup of cement dust.
- Use vacuum systems equipped with HEPA filters for dust collection.
4. Skin Protection
- Wash off cement from your skin immediately using water and mild soap. Avoid using harsh cleaners that can worsen irritation.
- Apply a barrier cream before handling cement to create a protective layer.
5. Emergency Response
- Eye contact: If cement gets in your eyes, rinse immediately with plenty of clean water for at least 15 minutes and seek medical attention.
- Skin burns: Flush the affected area with water and remove contaminated clothing. Consult a medical professional if burns persist.
- Inhalation: Move to fresh air and seek medical help if breathing difficulties occur.
Health Monitoring and Training
Employers have a responsibility to monitor the health of workers exposed to cement and ensure they receive adequate training.
1. Health Surveillance
Regular medical checkups can help detect early signs of respiratory or skin conditions. Employers should maintain records of workers’ health assessments.
2. Safety Training
- Teach workers about the risks associated with cement and the importance of PPE.
- Demonstrate proper techniques for handling and mixing cement to reduce exposure.
- Train workers to recognize symptoms of overexposure and respond appropriately.
Legal Requirements and Standards
1. OSHA Guidelines
The Occupational Safety and Health Administration (OSHA) has established standards for cement safety. Employers must comply with these regulations to protect their workers. Key requirements include:
- Providing PPE at no cost to employees.
- Implementing engineering controls to minimize dust.
- Ensuring proper labeling of cement bags with hazard warnings.
2. Hazard Communication (HazCom)
Under OSHA’s Hazard Communication Standard, employers must inform workers about the dangers of cement and provide Safety Data Sheets (SDS) for all cement products used on-site.
3. Silica Exposure Standards
Since cement contains crystalline silica, employers must adhere to OSHA’s permissible exposure limit (PEL) for respirable crystalline silica.
Tips for Reducing Cement-Related Hazards
- Wet Cement Carefully: Use tools to mix cement rather than bare hands to avoid direct skin contact.
- Automate Tasks: Where possible, use machinery for mixing and transporting cement to reduce manual handling.
- Work in Teams: Working in pairs or groups ensures prompt assistance in emergencies.
- Regular Maintenance: Inspect PPE and equipment regularly for wear and tear. Replace damaged items immediately.
- Encourage Reporting: Foster a culture where workers feel comfortable reporting hazards or safety concerns.
Innovations in Cement Safety
The construction industry is continuously evolving to improve safety. Some modern innovations include:
- Low-Dust Cement: Formulations designed to reduce airborne particles during mixing.
- Eco-Friendly Alternatives: Cement blends with reduced chromium content lower the risk of allergic reactions.
- Robotic Assistants: Machines designed to handle heavy lifting and repetitive tasks minimize human exposure to cement hazards.
Conclusion: Prioritizing Cement Safety in the Workplace
Safety when working with cement should never be an afterthought. By understanding the risks, implementing preventative measures, and adhering to legal requirements, employers can create a safer environment for their workforce. Workers must also take personal responsibility by wearing appropriate PPE and following safety protocols.
Remember, safety is everyone’s responsibility. Let’s build a stronger, safer construction industry together.
“Start Your Website Journey Today – Exclusive Hostinger Discounts!”

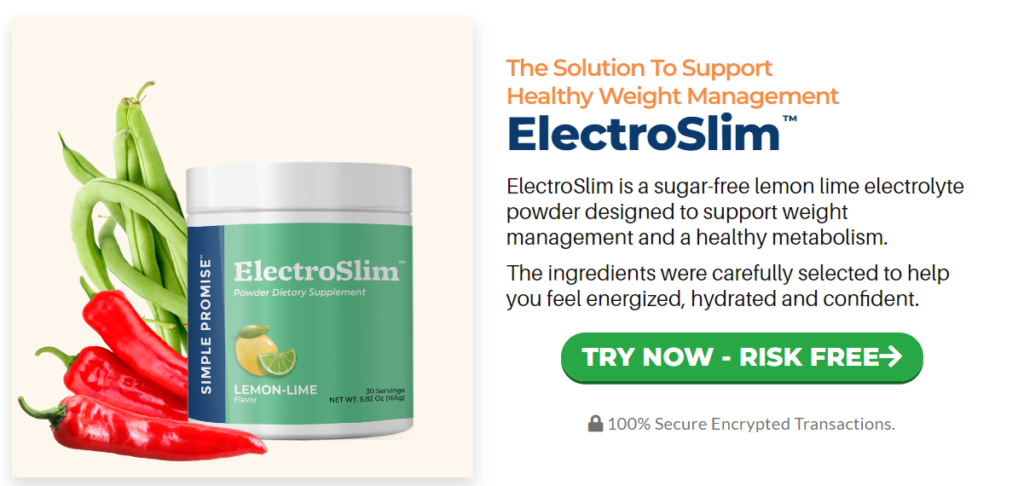

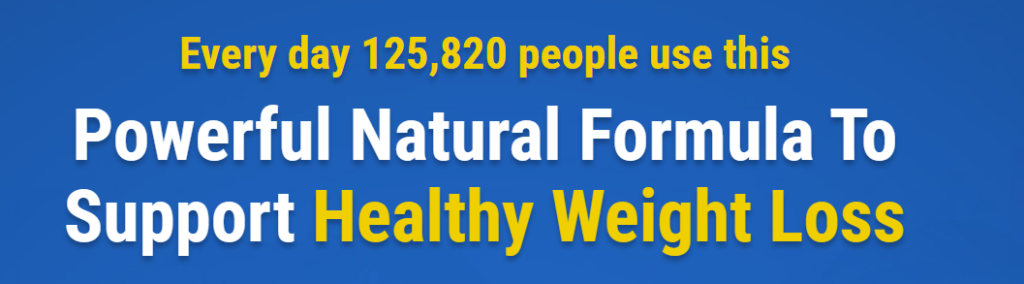

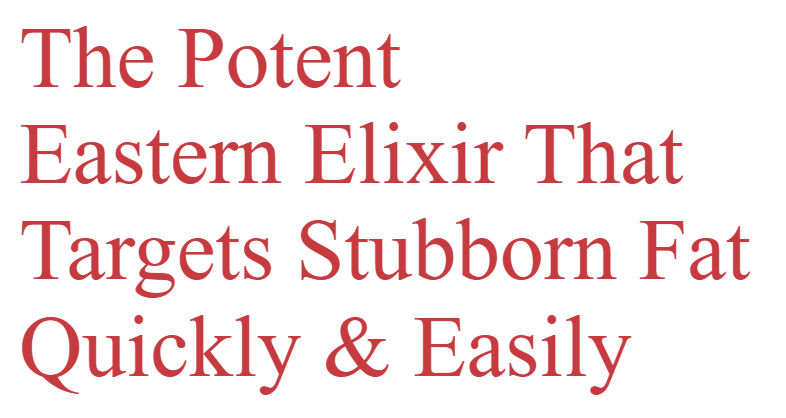
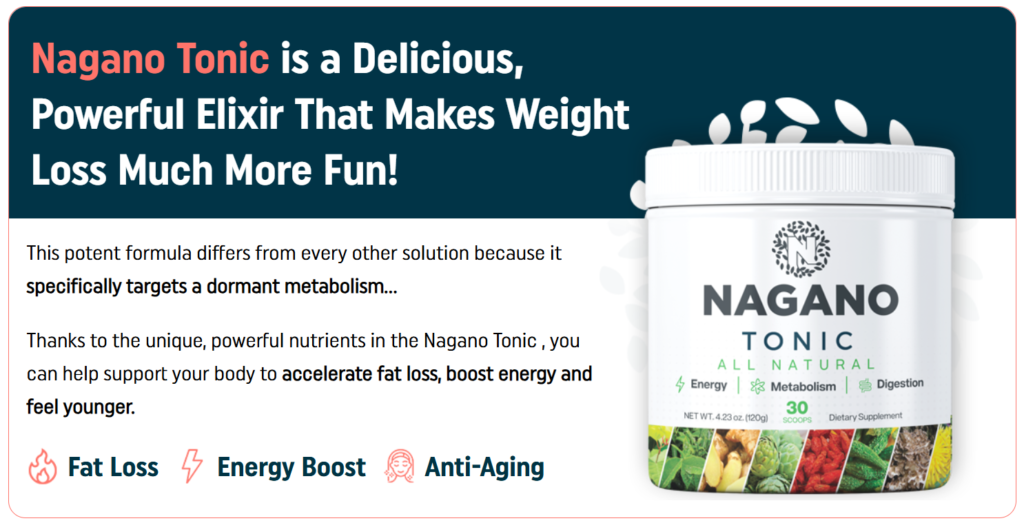