Statutory Duties of Factory Management
🏭 Introduction: Why Factory Safety Management is No Longer Optional
In an era where industrial growth is surging across India, workplace safety has become more than just a regulatory checkbox—it’s a strategic necessity. The Factories Act, 1948, and its subsequent amendments, make it abundantly clear: factory management holds a legal and moral obligation to ensure the health, safety, and welfare of its workers.
But here’s the thing: compliance isn’t just about avoiding penalties or inspections. It’s about building trust, reducing downtime, and fostering a culture where employees feel valued and protected.
In this blog, we’ll take a deep dive into the statutory duties of factory management in India, especially focusing on safety regulations, legal requirements, and practical steps you can implement right away.
⚖️ A Quick Look at the Governing Law: The Factories Act, 1948
The backbone of India’s industrial safety framework is the Factories Act, 1948. This law governs all factories employing 10 or more workers with power, or 20 or more workers without power.
Key Objectives of the Act:
- Ensure occupational health and safety
- Regulate working hours and conditions
- Enforce minimum welfare standards
- Mandate safety provisions and compliance mechanisms
Every factory owner, occupier, or manager must understand and follow the provisions of this Act to avoid legal liabilities and ensure a safe working environment.
🛡️ Statutory Duties of Factory Management in Safety: Section-Wise Breakdown
Let’s now explore the key responsibilities factory management must fulfill to stay compliant with Indian safety laws.
✅ 1. General Duties of the Occupier (Section 7A)
This is one of the most critical sections in the law.
Key Responsibilities:
- Ensure the health, safety, and welfare of all workers
- Provide and maintain safe systems of work
- Eliminate or minimize risks associated with machinery, equipment, and chemicals
- Conduct training programs and safety awareness sessions
- Prepare a written safety policy
💡 Best Practice: Periodically review and update your safety policy to reflect changes in machinery, workflow, or regulations.
✅ 2. Duties Related to Health (Sections 11–20)
These sections cover everything from cleanliness to ventilation.
Key Safety Requirements:
- Maintain clean working conditions
- Ensure adequate lighting and ventilation
- Provide safe drinking water
- Avoid overcrowding
- Prevent exposure to dust, fumes, and hazardous substances
🧼 Pro tip: Implement weekly hygiene audits and enforce cleanliness protocols in shared areas like toilets and canteens.
✅ 3. Safety Provisions (Sections 21–41)
This is where things get detailed and technical.
Key Safety Measures:
- Secure and fence dangerous machinery parts
- Train workers on safe machine operation
- Install emergency stop mechanisms
- Provide personal protective equipment (PPE)
- Ensure electrical safety
- Set up fire-fighting arrangements
- Use precautions for explosive or flammable materials
⚠️ Note: Accidents due to non-compliance with these safety provisions can lead to criminal liability for factory management.
✅ 4. Welfare Provisions (Sections 42–50)
Though not directly under “safety,” welfare measures significantly influence health and accident prevention.
Requirements Include:
- Clean and ventilated washrooms
- Accessible first-aid appliances
- Adequate restrooms, lockers, and canteens
- Creche facilities for women workers’ children
🏥 Pro tip: Conduct regular health check-ups for workers and maintain medical records.
✅ 5. Working Hours and Employment of Young Persons (Sections 51–69)
Ensuring that employees aren’t overworked or placed in risky roles they’re unfit for is a critical safety obligation.
Prohibited Practices:
- Employing children under 14
- Assigning hazardous duties to young workers
- Allowing overtime without proper rest intervals
⏰ Reminder: Proper work-rest cycles reduce fatigue-related accidents.
📋 Safety Audit & Risk Assessment: An Ongoing Duty
Merely meeting compliance once isn’t enough. The law expects factory managers to conduct:
- Routine safety audits
- Job hazard analysis (JHA)
- Risk mitigation planning
- Recordkeeping of accidents, near-misses, and remedial actions
📁 Documentation Tip: Maintain a digital safety compliance dashboard with audit trails.
🚒 Fire Safety and Emergency Response Plans
Every factory must be ready for emergencies—especially fire incidents.
Must-Have Protocols:
- Clear fire evacuation maps
- Regular fire drills
- Easily accessible fire extinguishers and hydrants
- Emergency exits with proper signage
- Designated Emergency Response Team (ERT)
🔥 Actionable Advice: Partner with local fire departments for mock drills and fire-safety workshops.
👷 Training and Supervision: Legal and Practical Mandate
Safety starts with awareness and education.
Legal Mandates:
- Conduct induction training for all new workers
- Provide job-specific safety instructions
- Offer refresher courses at regular intervals
- Appoint Safety Officers in units with 1000+ employees
📚 Pro tip: Use both online and on-ground training methods to maximize reach and retention.
📄 Display and Reporting Requirements
Indian law is particular about notice boards and documentation.
Display Requirements:
- Factory license and registration
- Emergency contact numbers
- Safety instructions and warning signs
- Standing orders (in applicable units)
Reporting Obligations:
- Notify Inspector of Factories about serious accidents
- Submit Form 18 in case of dangerous occurrences
- Maintain accident registers and Form 21
📝 Compliance Tip: Use automated compliance software to avoid missing deadlines.
🧑⚖️ Penalties for Non-Compliance: What’s at Stake?
If you think non-compliance is minor, think again.
Possible Consequences:
- Fines up to ₹2,00,000
- Imprisonment up to 2 years for serious breaches
- Factory license suspension or revocation
- Criminal charges in case of fatalities
💥 Avoid This: Ensure periodic internal audits and third-party safety inspections.
📈 Case Study: How Compliance Improved Safety in an Indian Manufacturing Unit
A leading auto-parts manufacturing unit in Pune reduced workplace injuries by 47% in one year after implementing:
- Digital safety audits
- Real-time PPE tracking
- Mandatory monthly safety training
- Worker feedback sessions
🎯 The result? Increased morale, fewer shutdowns, and higher operational efficiency.
✅ Factory Management Safety Checklist
Category | Checklist Item | Status |
---|---|---|
Health | Clean toilets, drinking water | ✅ |
Safety | Machine guarding, PPE provided | ✅ |
Fire | Alarms, exits, hydrants | ✅ |
Training | Induction & refresher programs | ✅ |
Legal | Licenses & notices displayed | ✅ |
Create your own custom checklist in Excel or Google Sheets for monthly reviews.
💬 Final Thoughts: Safety is Good Business
At the end of the day, safety is not just a legal requirement—it’s a leadership responsibility. A factory that prioritizes its workers’ well-being will see reduced attrition, better productivity, and a stronger brand reputation.
Factory managers and occupiers must realize: compliance is not a cost—it’s an investment in people, performance, and profit.
So if you haven’t already, start reviewing your safety framework today. Your workers—and your bottom line—will thank you.
📚 Recommended Resources
- Factories Act, 1948 – Full Text
- ILO Guidelines on Occupational Safety
- Ministry of Labour and Employment – India
💬 Join the Conversation
Have you implemented any unique safety practices in your factory? What challenges have you faced with compliance?
Drop a comment below or share this post with your HR, Operations, and Safety teams. Let’s build safer workplaces—together.
“Start Your Website Journey Today – Exclusive Hostinger Discounts!”

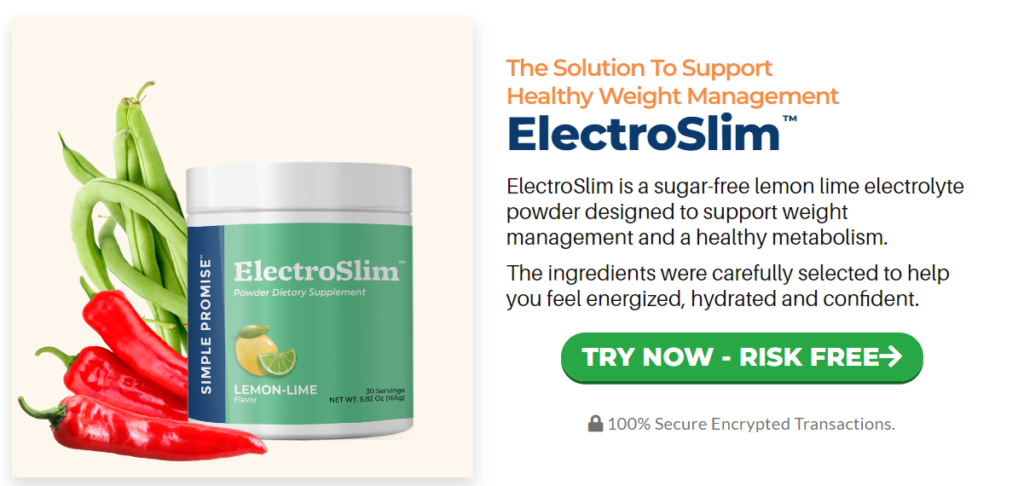

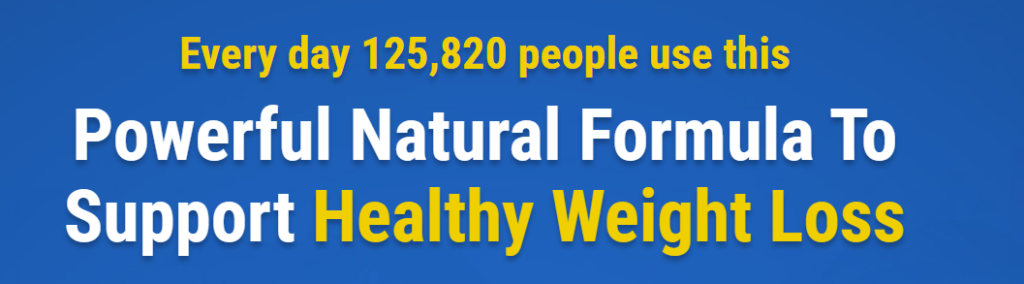

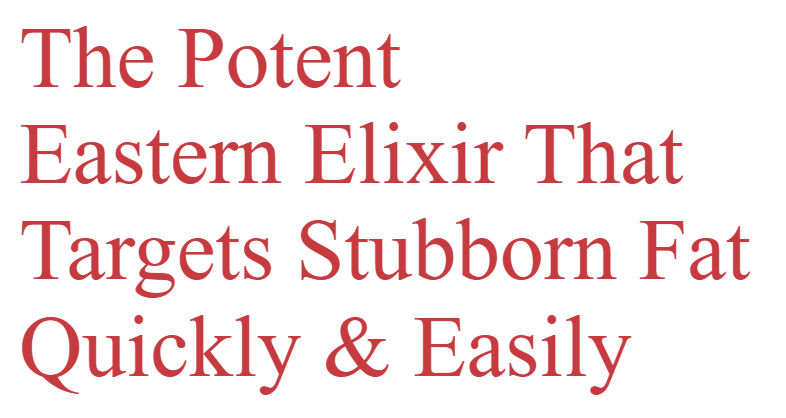
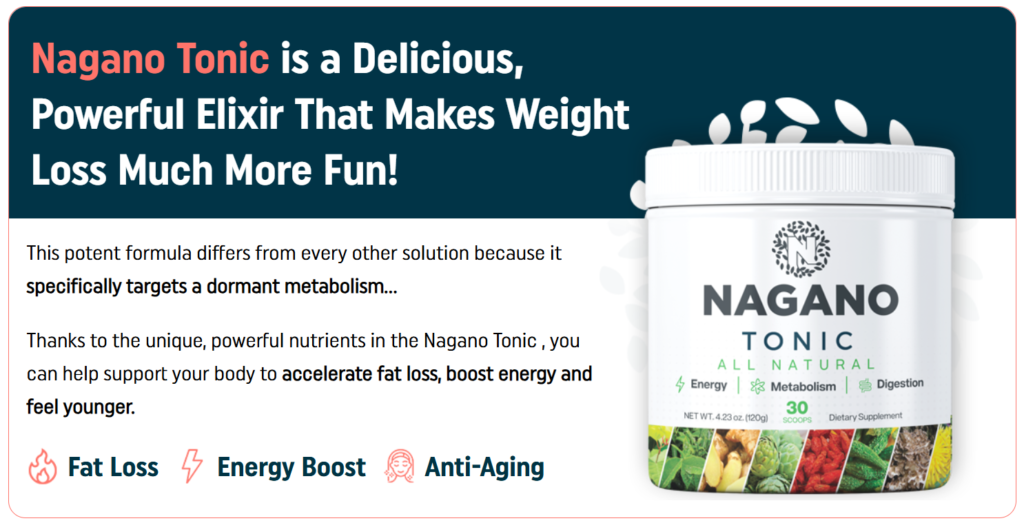