The field of safety psychology is relevant to both employers and employees. Workplace accidents result from errors on either side. While the primary responsibility for ensuring safe working conditions, a secure environment, and protective equipment rests with the employer, employees play a crucial role in accident prevention through psychological awareness and proper use of protective gear. Since employees are greater in number, the likelihood of human errors increases. Therefore, it is their individual and collective duty to minimize such errors, prevent accidents, and uphold workplace safety.
Current psychological safety challenges can be categorized into two areas: those faced by employers and those faced by employees. Ultimately, these issues also impact society and the nation as a whole.
Employer’s Problems:
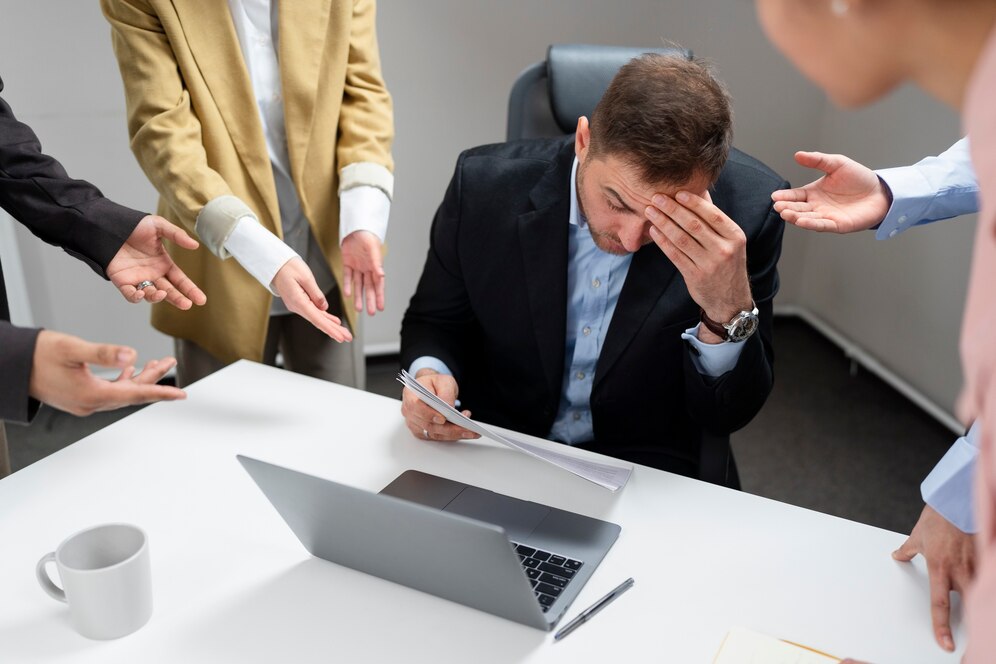
Employers not only expect production targets from their employees but also attitudes, loyalties, and cooperative efforts. This interest is as significant to psychologists as employers’ desires to understand their employees’ resources, motivations, and capabilities. Issues like worker disobedience, indiscipline, sabotage, misuse of safety equipment, neglecting safety protocols, and engaging in strikes or slowdowns that compromise safety are psychological concerns troubling employers today. While employers seek government assistance, the real solution lies in self-discipline and personal responsibility, as external intervention has limited impact if individuals are unwilling to change.
Although the Factories Act of 1948 includes provisions to penalize workers for safety violations, governments are often hesitant to enforce these laws. Even when enforced, witnesses are reluctant to testify due to fear of retaliation. This atmosphere of deliberate indiscipline poses a significant challenge for psychologists aiming to promote safety. Trade unions should also play a role in addressing this issue.
Workers must realize that their safety and that of others depend on their actions. Safety is a matter of cooperation and constructive behavior, not negligence or destruction. Failing to uphold safety standards can lead to serious injuries or fatalities, and no amount of compensation can replace a lost life. Protecting lives, machinery, production, and the environment is crucial, as any harm ultimately results in national loss. Maintaining safety and addressing problems in a safe environment is essential. Performing safety duties diligently and ensuring that everyone enjoys their rights is the best way to influence human behavior toward safety. Regular HRD training by employers can be beneficial.
Beyond their duty to workers, recent legislation over the past decade, such as the Factories Act, Environment (Protection) Act, Public Liability Insurance Act, and Chemical Accidents (EPPR) Rules, has expanded employers’ responsibilities to include the public. Employers are now required to inform the general public about hazards, controls, and their roles in emergencies. Any citizen or member of a Crisis Group can request this information. However, employers often hesitate to provide such information due to concerns about liability. In the event of a major accident affecting the public, authorities may prosecute non-compliant employers. The best solution is voluntary compliance with these laws.
Employee’s Problems:
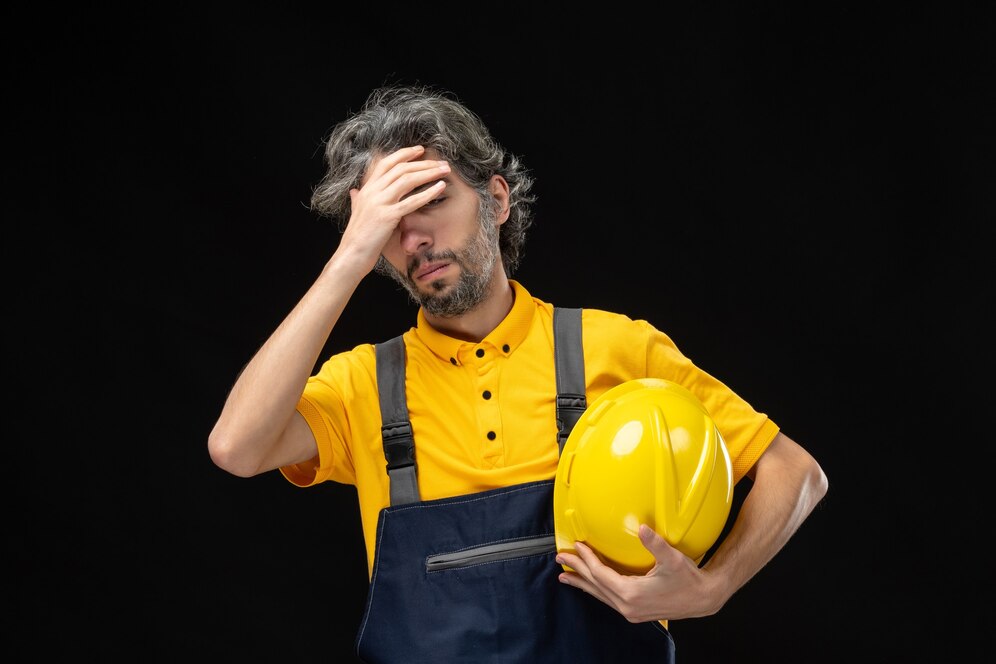
Employees expect more from their employers than just wages—they seek security, opportunities for growth, and workplace protection. These expectations are just as important to psychologists as employees’ personal desires for self-expression, recognition, and favorable working conditions.
However, in many small and medium-sized factories, these expectations are rarely met. Poor, uneducated, unorganized, and often contract workers continue to face exploitation, enduring long hours in unsafe and unhealthy work environments. Even educated workers often receive unsatisfactory wages, leading to low morale. Trade unions could play a role in shifting these attitudes, but even basic legal requirements for health, safety, and welfare are frequently neglected. As a result, many workers lack recognition, security, and opportunities for growth, working merely out of economic necessity or desperation.
The role of Safety Officers remains largely undervalued by many employers, further discouraging and demotivating those responsible for workplace safety. It is crucial to recognize and prioritize the contributions of safety personnel.
Despite existing factory and safety regulations, working conditions for many employees remain poor. While a few well-managed factories maintain safer environments, most require significant improvements. Many workplaces lack machine guards, covered floor openings, safe access points, and functional safety devices. Occupational illnesses often go undetected, while hazardous conditions such as dust, fumes, gas emissions, and pollution persist. Dangerous machinery, pressure vessels, and chemical equipment frequently fail to meet safety standards, leading to numerous accidents. Yet, workers seldom complain, having accepted these conditions as the norm with little hope for change.
Who is responsible for this situation? The blame is often shifted between different parties. Employers claim they provide safety measures, but workers fail to maintain them. Some argue they lack the funds for expensive safety equipment and expect government subsidies. Workers, on the other hand, insist that safety devices are either absent or malfunctioning, with their complaints falling on deaf ears. Factory inspectors enforce regulations, but their focus is often on non-safety violations, and due to staff shortages and excessive workload, consistent follow-up is rare. This cycle of blame creates deep-rooted psychological challenges within the workplace.
However, blaming one another will not resolve the issue. Every party shares some responsibility. It is, without question, the primary duty of employers to provide and maintain workplace safety. Safety budgets should be incorporated from the outset and allocated annually. Establishing safety committees that include worker representatives can help review and improve safety conditions. Unsafe practices and hazardous conditions must be addressed through collective efforts. Workers, supervisors, and all employees should actively engage in fostering a culture of safety. Preventive and corrective maintenance should be conducted regularly.
Factory inspectors must enforce safety compliance rigorously while also offering guidance and education on workplace safety. Trade unions should contribute by raising safety awareness and promoting training initiatives. Ultimately, fostering a proactive and responsible attitude towards workplace safety is essential to improving human behavior in this area.
“Start Your Website Journey Today – Exclusive Hostinger Discounts!”

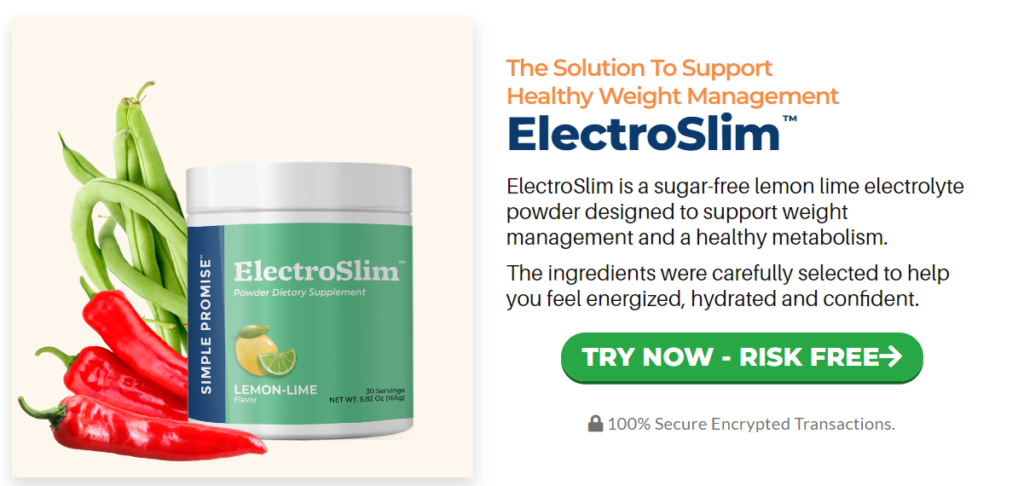

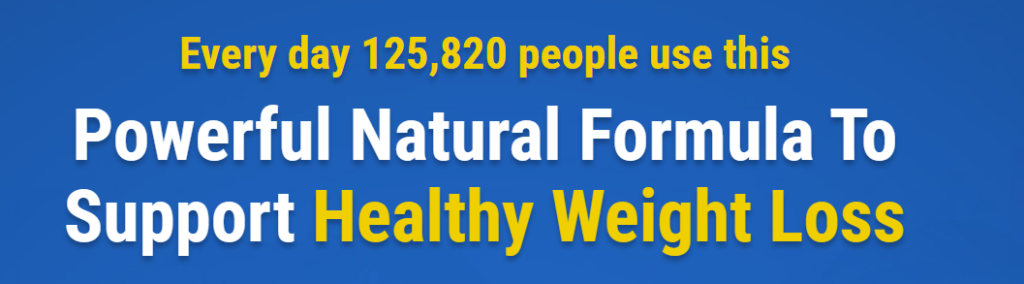

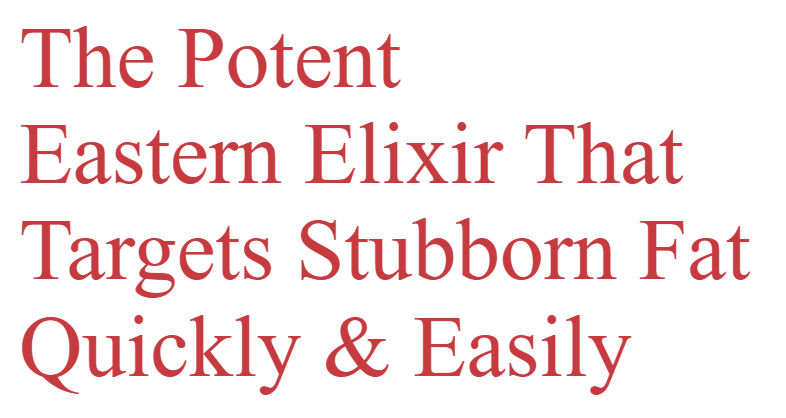
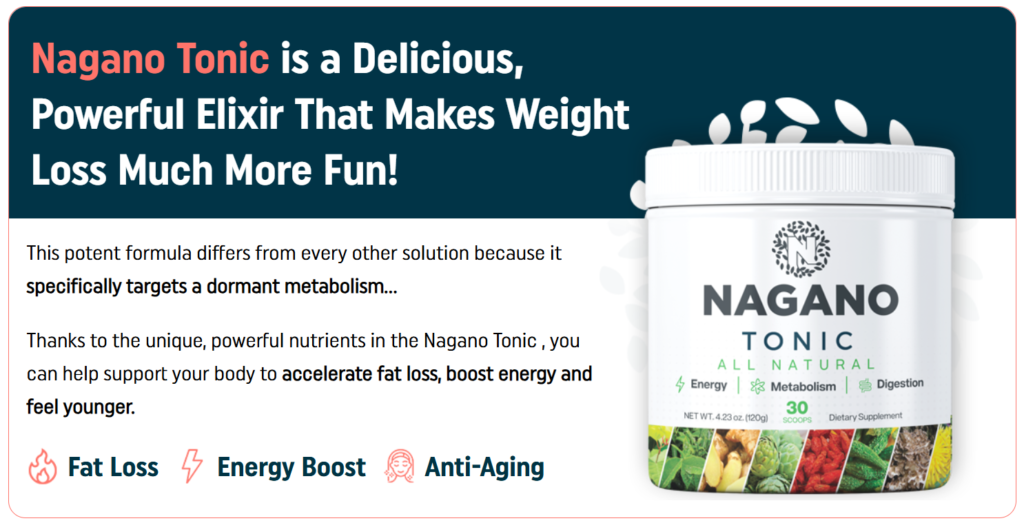