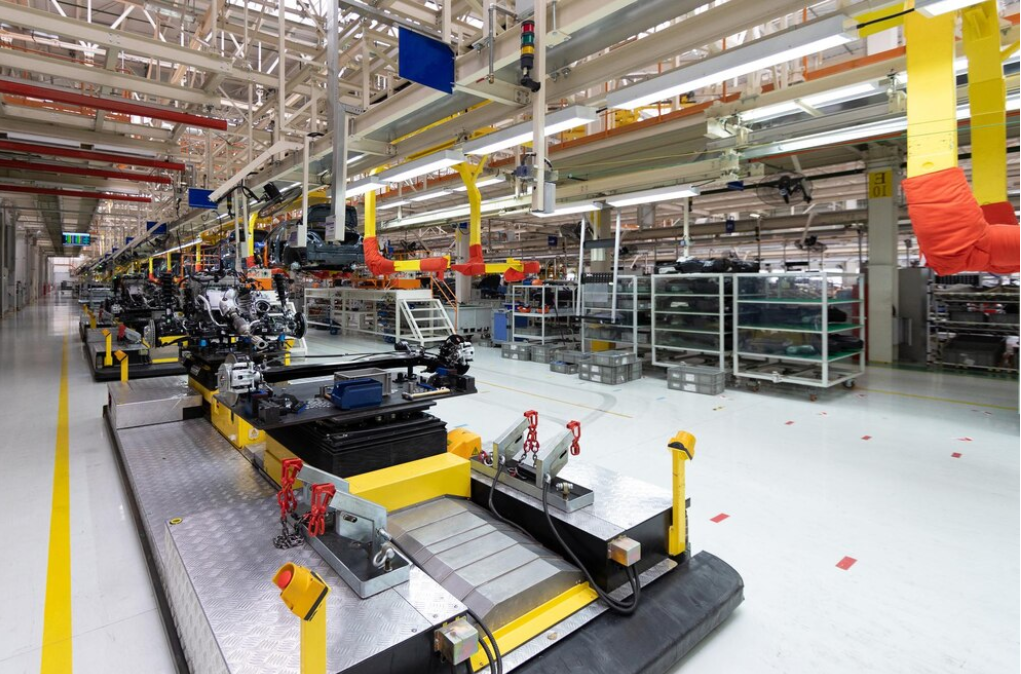
•Good housekeeping is good business.
•Good housekeeping and profitable operation are inseparable companions.
•Industrial housekeeping is the process of maintaining all work and storage area clean, neat and orderly combined with elimination of all non-essential materials and equipments.
•The quality of housekeeping in a plant, workplace is an excellent indication of the efficiency of its operation and of the effectiveness of maintenance.
Approach shall be – system oriented and not visitor /Audit oriented. That means 5S system should be so strong that plant/office/workshop will always remain in a presentable form whether visitors/auditors are there or not.
FACTORS GOVERNING HOUSEKEEPING
•Proper layout of equipments
•Correct material handling & storage
•Cleanliness & orderliness
•Elimination of unnecessary materials
•Provision of suitable drip trays waste bins etc.
•Training/administration
IMMEDIATE & LONG RANGE RESULTS
OF GOOD HOUSEKEEPING
•Higher Employee Morale :- Clean surroundings and comparative freedom from injury improve employee attitudes.
•Increases Production :- Once excess material, loose tools, and other obstructions to production are removed, orderly and business-like methods can function without undue interference or delay.
•Saves Production Time :- There is no need to search for tools, parts or materials.
•Betters use of floor space :- Clear areas permit free movement of operators and afford repairmen easy access to machines and equipment.
•Open aisles permit faster traffic with fewer collisions.
•Lowers Accident Rates :- Sufficient work space and elimination or tripping, slipping, bumping against, being struck by, dropping and caught between object hazards means fewer injuries.
•Reduces Fire Hazards :- Fire result from, or are spread by poor housekeeping conditions. Good housekeeping is vital to an effective fire prevention programme.
•Reduces Operating Costs :- Once a department is clean and a housekeeping system has been established, less time and effort are required to keep it clean.
•Improves Production Control :- Material and parts do not get lost or mixed-up. Checking operations and recording data are easier.
•Conserves Materials &Parts :- Unused materials, including spoilage and scrap, are easily and quickly removed to the proper place.
“5 S” HOUSEKKEEPING CONCEPT
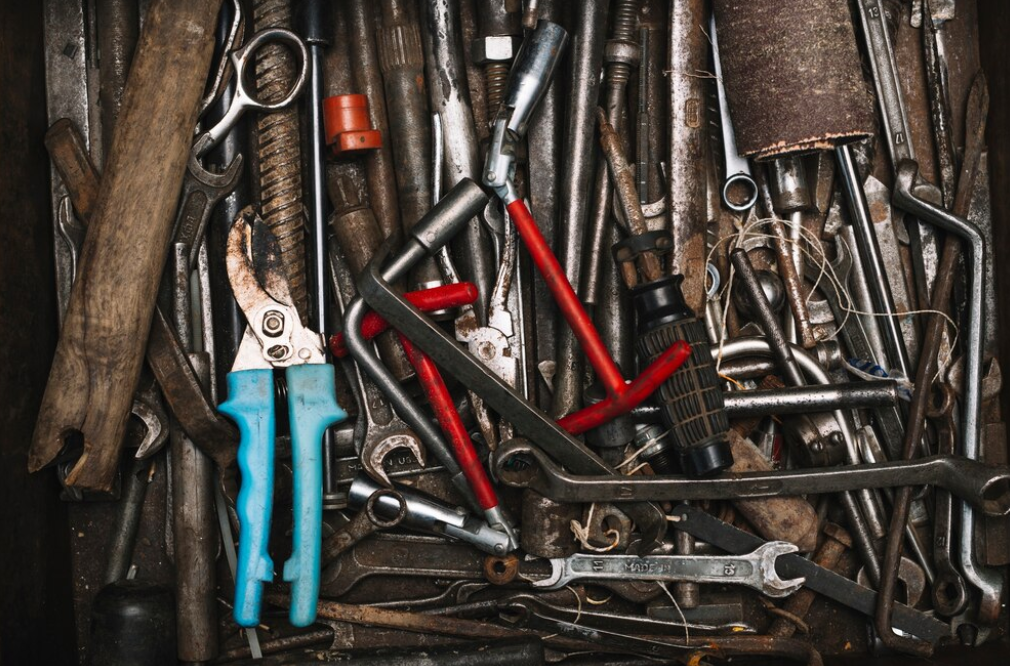
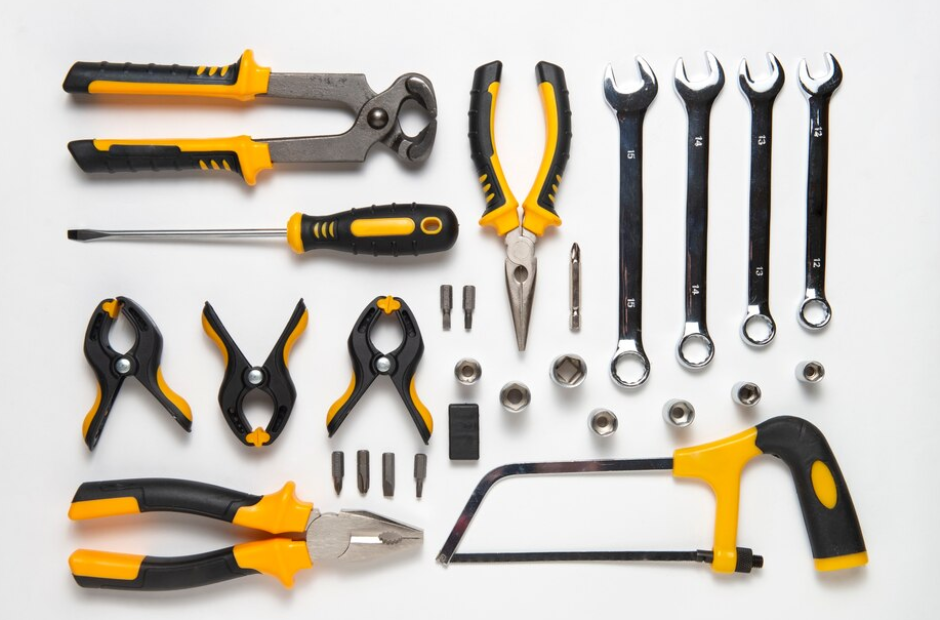

5 S” called by Japanese as they start with “S”. It is a time tested
& scientific way to improve the housekeeping .
The five steps are :-
1.SERI (Sorting out)
2.SEITON ( Systematic Arrangement)
3.SEISO ( Cleaning )
4.SEIKETSU ( Standardization)
5.SHITSUKE ( Self- Discipline).
1. SERI (Sorting Out)
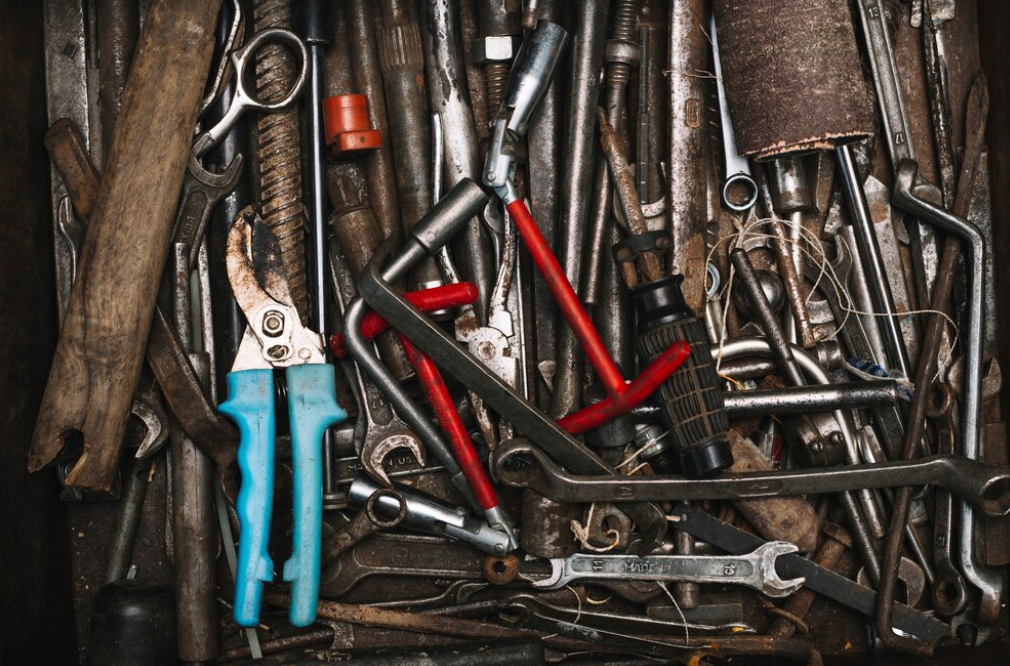
It means looking at all items, articles, tools or material around the work area; collecting all the items and segregating them in three categories:-
(a) Okay & useful materials.
(b) Materials, which can be made useful after some repairs or
rework (In maintenance workshops/stores etc.) (c) The rejected or unusable material.
2. SEITON ( Systematic Arrangement)
It means storing all the usable items at a designated location so that they are easily accessible and can be conveniently used.
The golden rule to be remembered while storing is “ A place for everything and everything in its place”.
3. SEISO ( Cleaning )
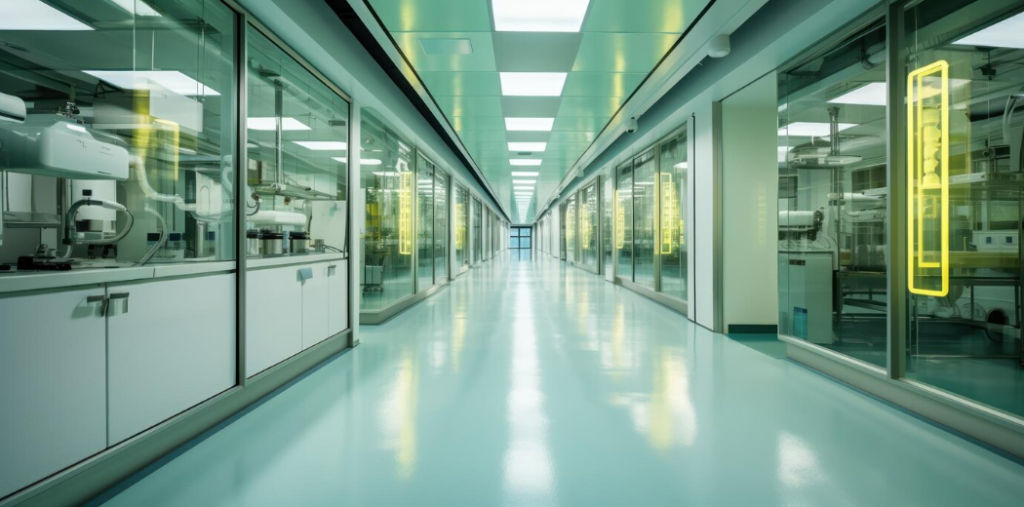
It means cleaning and maintaining the office, work place, tools, machines and equipments in near condition.
4. SEIKETSU ( Standardization)
It lays emphasis on consistency and repetition of the earlier 3S’s to prevent backsliding. It is standardising in short and involves a lot of visual management and colour coding so that abnormalities show up for themselves.
5. SHITSUKE ( Self- Discipline)
Even after achieving high standards of cleanliness, systematic arrangement, the members of the organization should exhibit a strong sense of self-discipline. It is imperative to follow the rules and regulations prescribed for good quality, safety and productivity.
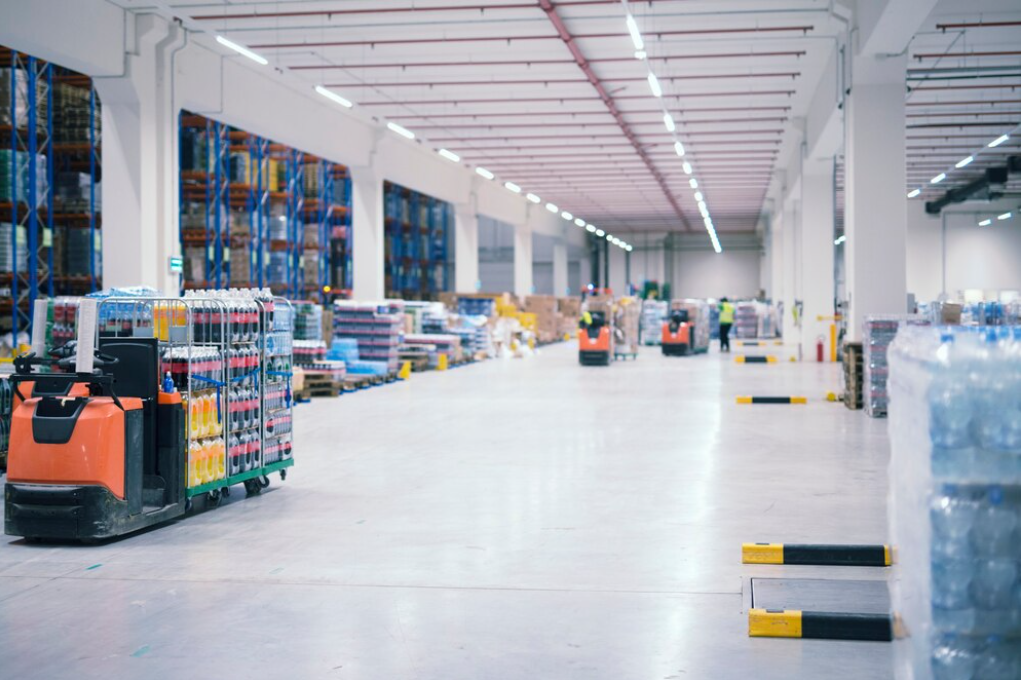
EVALUATION GUIDELINES
•SORTING OUT
Check whether all the items, articles, tools or materials are segregated in three categories (i) Useful material (ii) Materials which can be made useful after some repairs (in maintenance workshops/stores) (iii) The rejected or unusable material. No unwanted material should be lying in the work place.
Areas to be considered under “Sorting Out” step :-
(a) Sorting Out in the field.
(b) In Inst./Mech./Elect/Process Stores & Workshops.
(c) In Sub-station, Control Room & Service Building.
• Evaluation Criterion | ||
Excellent | If, the Sorting out is done at all places and no unwanted material and items found at any place. | |
Very Good | If, the Sorting out is done at most of the places. | |
Good | If , the Sorting out is done at some places while the Sorting out is not proper at other places. | |
Average | If, the Sorting out is done only at few places. | |
Poor | If, no Sorting is done and the unwanted materials/items are lying everywhere. | |
Note: If, the usable material/items of some departments are found in other departments workplace/storages, it shall be treated as improper sorting. |
• SYSTEMATIC ARRANGEMENT The following areas are to be checked under this step. (a) ARRANGEMENT OF USABLE MATERIALS IN FIELD & PROCESS STORE The usable items like additive drums, bags, product, chemicals etc. shall be checked. | ||
Evaluation Criterion | ||
Excellent | If, the usable material is arranged systematically at all the places. | |
Very Good | If, the usable material is arranged properly at most of the places. | |
Good | If, the usable material is arranged systematically at some places but proper arrangement is required at some other places also. | |
Average | If, the usable material is arranged only at few places. | |
Poor | If, the usable material is lying in the haphazard manner in the field and process store. |
(b) SCRAP DISPOSAL SYSTEM IN THE FIELD The Scrap Disposal System in the field shall be checked | ||
Evaluation Criterion | ||
Excellent | If, the place/bins are provided for all types of scrap and the scrap is segregated and kept properly in the bins. | |
Very Good | If, the place/bins are provided for all the scrap and the scrap is kept properly at most of the places/bins. | |
Good | If, the place/bins are provided for most of the scrap and the scrap is segregated and kept properly at some places/bins. | |
Average | If, the place/bins are provided for some of the scrap and the scrap is segregated and kept properly only at few places/bins. | |
Poor | If, no proper designation of bins/places for scrap and scrap is lying without any segregation. |
(c ) ARRANGEMENTS OF TOOLS/MATERIALS IN INST./ELECT./ MECH STORES & WORKSHOPS Systematic segregation and arrangement of tools/materials shall be checked in the maintenance stores &workshop. | ||
Evaluation Criterion | ||
Excellent | If, all the tools/materials are arranged systematically. | |
Very Good | If, most of the tools/material are arranged systematically. | |
Good | If, some of the tools are arranged systematically while some other are also to be properly arranged. | |
Average | If, only few tools/materials are arranged properly. | |
Poor | No proper arrangement of tools/materials. |
(d ) ARRANGEMENT IN SUB-STATION, CONTROL ROOM AND SERVICE BUILDING. The arrangement of furniture, cabinet, racks, documents etc. shall be checked. | ||
Evaluation Criterion | ||
Excellent | If, all items are systematically arranged. | |
Very Good | If, most of the items are systematically arranged. | |
Good | If, some items are systematically arranged while the some others also to be properly arranged. | |
Average | If, only few items are properly arranged. | |
Poor | No proper arrangement of any item. |
• CLEANING The following areas shall be assessed under this step. Cleaning in the field/process area. In Mech./Inst.Elect. Workshop/Store In service Building, control rooms, sub-stations, entrance, parking and assembly points etc. | ||
Evaluation Criterion | ||
Excellent | If, the floor, machines, equipments, structures, stairways et. Are thoroughly cleaned. In case of leakage, proper care has been taken at all the places. | |
Very Good | If, most of the floor area, equipments, structures, machines, stairways etc. are thoroughly cleaned. In case of leaks, proper care is taken at most of the places. | |
Good | If, some of the area, equipments, structures, machines, stairways etc. are thoroughly cleaned while the cleaning at other places is not satisfactory. In case of leaks, proper care is taken at some places only. | |
Average | Only at few places, cleaning is good and a few machines, equipments are cleaned. In case of leak, are is taken at few places only. | |
Poor | Cleaning is not good at all the places. No proper care in case of leaks. |
• STANDARDIZATION Visual management and proper colour coding shall be checked. The following areas shall be assessed under this step. (a) PROPER BOARDS/COLOUR CODING IN FIELD/PROCESS AREA Check for proper boards at all the places. Relevant work instructions should be displayed in the field. All process lines/ vessels/ equipment/machines should have identification & proper color coding. | ||
Evaluation Criterion | ||
Excellent | If, proper boards, color coding is done at all the places. | |
Very Good | If, proper boards, color coding is done at most of the places. | |
Good | If, proper boards, color coding is done at few places but it is required at some more places. | |
Average | If, proper boards, color coding done at few places only | |
Poor | If, no boards displaced and improper or no color coding. |
(b) PROPER IDENTIFICATION PLATES, COLOUR CODE IN ELECT./ INST/ MECH. STORES. Check for proper identification plates, color code provided for the segregated and arranged tools, materials and other articles. | ||
Evaluation Criterion | ||
Excellent | If, proper identification plates, color coding done for all items. | |
Very Good | If, proper identification plates, color coding done for most of the items, | |
Good | If, proper identification plates, color coding done for some items but it is required at some more places. | |
Average | If, proper identification plates, color coding done for few items. | |
Poor | If, no proper identification plates or color coding done. |
(c) PROPER IDENTIFICATION OF DOCUMENTS AND OTHER ITEMS IN CONTROL ROOM, SUB-STATION & SERVICE BUILDINGS. Check whether all the arranged documents and items have identification. All the filling racks/cabinets should have proper list of files/documents. | ||
Evaluation Criterion | ||
Excellent | If, all racks/cabinets, documents and other items have identification. | |
Very Good | If, some racks/cabinets/documents have identification but some other also to be given proper identification. | |
Good | If, some racks/cabinets/documents have identification but some other also to be given proper identification. | |
Average | If, only few racks/cabinets and documents have identification. | |
Poor | If, no racks/cabinets and documents have any identification. |
• DISCIPLINE The following areas shall be checked under this step. (a) USE OF PERSONAL PROTECTIVE EQUIPMENTS (PPE’S) Check whether all employees, contract workers are wearing helmets, safety shoes, and other required Personal Protective Equipments (PPE’s). First –aid-boxes should also be checked. | ||
Evaluation Criterion | ||
Excellent | All employees/contract workers are wearing required Personal Protective Equipment (PPE’s). | |
Very Good | If, most of the employees/contract workers are wearing Personal Protective Equipments (PPE’s), except a few exceptions. | |
Good | If, most of the employees/contract workers are wearing Personal Protective Equipments (PPE’s). | |
Average | If, some of the employees/contract workers are wearing Personal Protective Equipments (PPE’s) and some are not wearing. | |
Poor | If, no or very few employees/contract workers wearing Personal Protective Equipments (PPE’s) |
(b) WORK PERMIT SYSTEM, INTERLOCKS CHECKING/BYPASS REGISTER Work permit system and records or interlocks checking and bypass should be maintained. | ||
Evaluation Criterion | ||
Excellent | If, all aspects of all work permits are taken care of interlocks/records and bypass registers maintained. | |
Very Good | If, all aspects of all work permits are taken care of except a few exception, interlocks records and bypass registers maintained. | |
Good | If, for most of the work permits, all the aspects are taken care of interlock records and bypass register maintained. | |
Average | If, only for some work permits, most of the aspects are taken care of, some records of interlock and bypass maintained. | |
Poor | No proper work permit system, no proper record of interlocks/bypassing. |
(c) UPKEEPING OF FIRE FIGHTING/SAFETY EQUIPMENTS All fire fighting and safety equipments/items like deluge systems, manual call points, fire monitors and extinguishers, safety showers, LEL sensors, smoke/heat detectors and other safety items shall be checked for healthy condition | ||
Evaluation Criterion | ||
Excellent | If, all fire fighting/safety equipments are in healthy condition. | |
Very Good | If, all fire fighting/safety equipments are in healthy condition, except a few exceptions. | |
Good | If, most of the fire fighting/safety equipments are in healthy condition except a few exceptions. | |
Average | If, some of the fire fighting/safety equipments are in healthy condition while some are not. | |
Poor | If, no or few fire fighting/safety equipments are in healthy condition. |
•Evaluation Method
–The level of housekeeping of the plant shall be assessed on the basis of marks obtained from the total 100 marks.
–All the five steps shall be given equal weightage for plants.
–Every point under each step shall be evaluated on five levels of scale I.e. Excellent, Very Good, Good, Average & Poor.
Excellent | 4 |
Very Good | 3 |
Good | 2 |
Average | 1 |
Poor | 0 |
•Evaluation Method
–The plants shall be placed under the five levels of housekeeping based on the total marks obtained from all the five steps.
LEVEL | HOUSEKEEPING RATING | % OF MRKS OBTAINED |
I | Excellent | 91-100 |
II | Very Good | 71-90 |
III | Good | 51-70 |
IV | Average | 31-50 |
V | Poor | 0-30 |
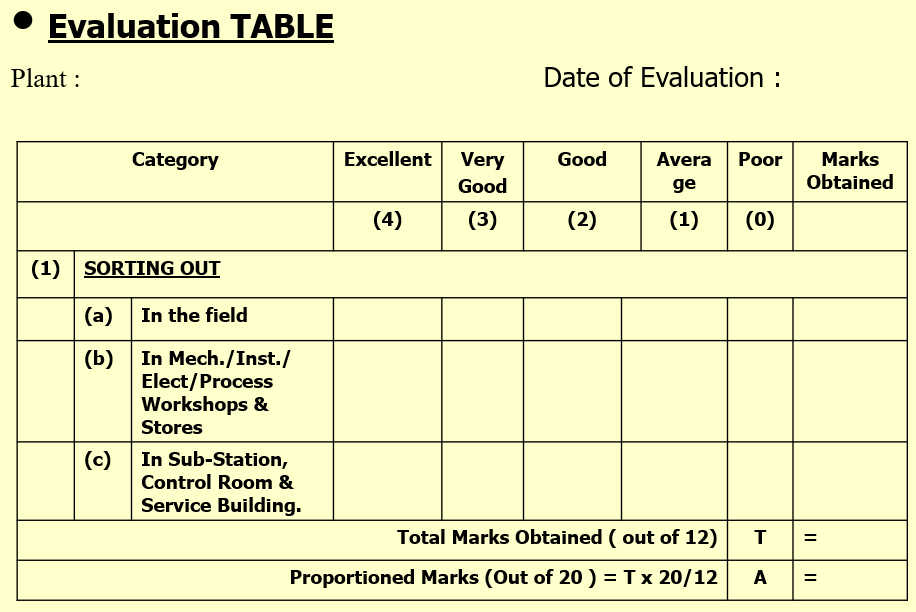

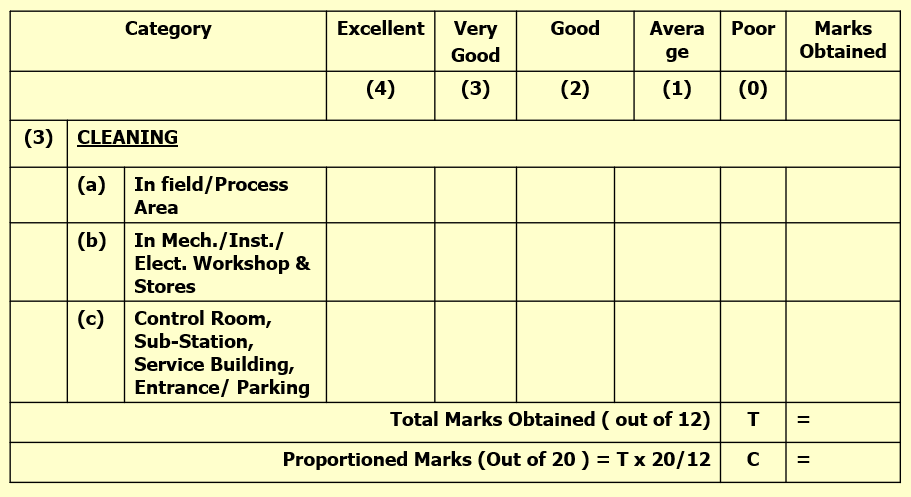
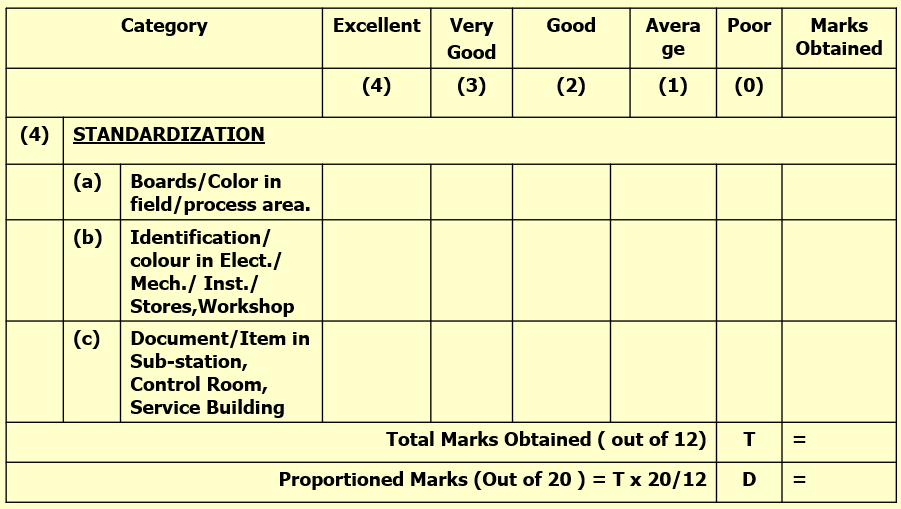
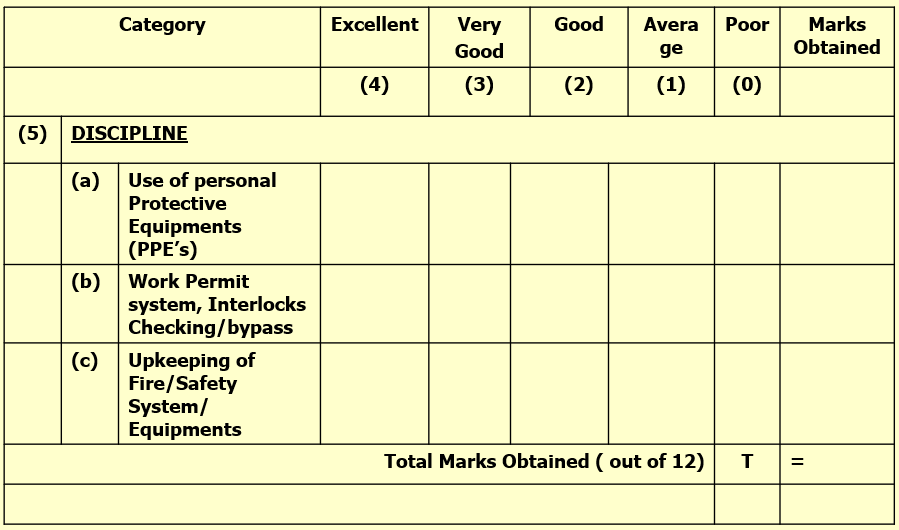
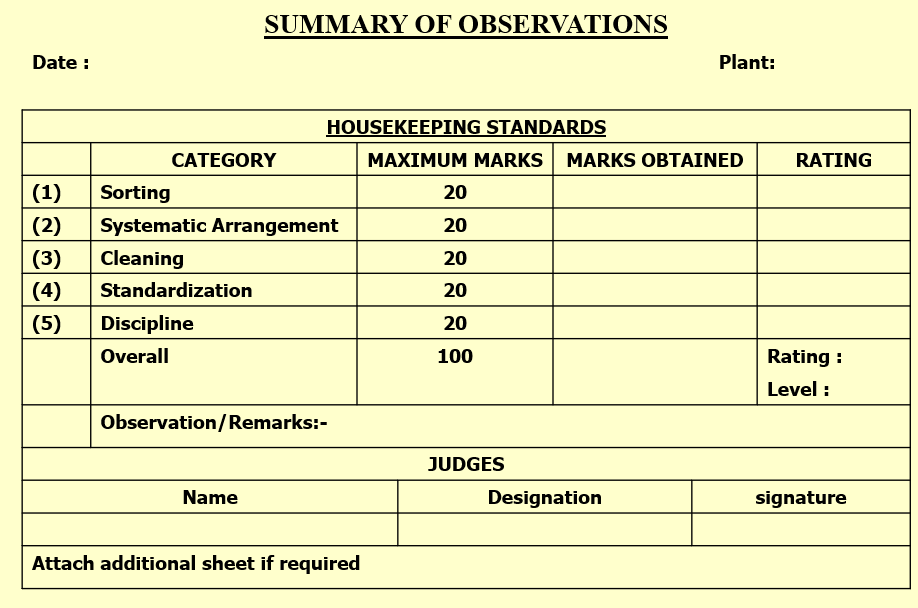
Remember
HOUSEKEEPING IS SAFE KEEPING
AND
GOOD HOUSEKEEPING MEANS
THERE IS A PLACE FOR EVERYTHING
AND EVERYTHING IS IN ITS PLACE.