Lead Exposure: Understanding and Preventing Risks in the Workplace
Lead exposure remains one of the most significant occupational hazards across various industries. Despite increased awareness and regulatory measures, many workers continue to face risks associated with this toxic metal. This article will discuss the dangers of lead exposure, its health impacts, industries where it is prevalent, and strategies to mitigate its risks. Our aim is to provide actionable insights that emphasize workplace safety and highlight the importance of employee health.
What is Lead Exposure?
Lead is a naturally occurring heavy metal found in the Earth’s crust. It has been widely used in various industries due to its malleability, resistance to corrosion, and conductivity. However, prolonged exposure to lead can cause serious health issues, particularly when it accumulates in the body over time.
How Lead Exposure Occurs
Exposure to lead primarily happens through inhalation of lead dust, fumes, or ingestion of contaminated substances. In occupational settings, employees working with materials like lead-based paints, batteries, and certain manufacturing processes are at heightened risk. Even though regulations have limited the use of lead in many products, older buildings and industrial environments may still pose significant exposure risks.
Health Risks Associated with Lead Exposure
One of the most critical aspects of workplace safety is understanding the health implications of lead exposure. Lead is toxic to virtually every organ system in the body, and its effects can range from mild to severe depending on the duration and level of exposure.
Short-term Effects
Acute lead exposure, which occurs over a short period, can result in symptoms such as:
- Fatigue
- Nausea and vomiting
- Muscle pain and cramps
- Difficulty concentrating
Long-term Effects
Chronic exposure to lead, even at low levels, is far more dangerous. It can lead to:
- Neurological disorders, such as memory loss and cognitive decline
- Kidney damage
- Cardiovascular issues like hypertension
- Reproductive problems, including infertility
- Developmental delays and learning difficulties in children exposed to lead via secondary contamination from adults
It’s crucial for employees and employers to recognize these risks and implement strategies to protect health and safety in workplaces where lead exposure is possible.
Industries with High Risk of Lead Exposure
Certain sectors are more prone to lead exposure risks due to the nature of their operations. Employers in these industries must take proactive steps to mitigate the hazards and comply with occupational health and safety regulations.
1. Construction and Renovation
Workers involved in the demolition of older buildings, repainting, or restoration projects often encounter lead-based paints and materials. Sanding, welding, or cutting these materials can release toxic lead dust into the air.
2. Battery Manufacturing and Recycling
The production and recycling of lead-acid batteries expose workers to high concentrations of lead. Ensuring proper ventilation and protective equipment is vital in such environments.
3. Smelting and Foundries
Employees in smelting facilities handle raw lead materials, creating an environment with elevated risks of inhalation and skin exposure.
4. Shipbuilding
Lead exposure is common in shipbuilding, especially in older vessels where lead-based paints and other materials are prevalent.
5. Ceramics and Pottery
Lead is sometimes used in glazes and pigments in ceramics. Workers who mix or apply these glazes risk inhaling fine lead particles.
Recognizing Lead Exposure Symptoms
Early detection of lead poisoning is critical to minimizing its long-term impacts. Workers and employers must be vigilant about the following signs:
- Persistent headaches
- Abdominal pain
- Loss of appetite
- Mood swings or irritability
- Anemia
If any of these symptoms are noticed, immediate medical evaluation is essential. A blood lead level (BLL) test is a reliable way to determine the extent of lead exposure.
Regulatory Standards for Lead Safety
Governments and health organizations worldwide have implemented strict regulations to limit occupational lead exposure. In the United States, the Occupational Safety and Health Administration (OSHA) mandates permissible exposure limits (PELs) to ensure employee safety.
OSHA Lead Standards
OSHA has set the following standards for workplace lead exposure:
- Permissible Exposure Limit (PEL): The maximum allowable airborne concentration of lead is 50 micrograms per cubic meter of air (µg/m³) over an 8-hour workday.
- Action Level (AL): When airborne lead reaches 30 µg/m³, employers must implement additional safety measures, including medical surveillance and exposure monitoring.
Compliance Requirements
Employers must:
- Conduct regular air monitoring.
- Provide personal protective equipment (PPE).
- Implement engineering controls, such as ventilation systems.
- Offer regular medical exams and blood lead testing for employees at risk.
How to Prevent Lead Exposure in the Workplace
Prevention is the cornerstone of workplace safety when it comes to lead exposure. Here are practical steps employers and workers can take to minimize risks.
1. Implement Engineering Controls
Engineering controls are one of the most effective ways to reduce lead exposure. These include:
- Installing proper ventilation systems
- Using sealed enclosures for processes that generate lead dust or fumes
- Employing wet methods to suppress dust
2. Provide Personal Protective Equipment (PPE)
PPE serves as the last line of defense for workers exposed to lead. This includes:
- Respirators
- Disposable gloves
- Protective clothing that can be removed before leaving the worksite
3. Promote Hygiene Practices
Encouraging good hygiene reduces secondary exposure. Employees should:
- Wash hands and face before eating, drinking, or smoking
- Shower and change clothes before leaving the workplace
- Use separate lockers for work and personal clothes
4. Train Employees on Lead Safety
Regular safety talks and training sessions help employees understand the risks of lead exposure and the importance of protective measures.
5. Conduct Regular Monitoring
Employers must frequently assess lead levels in the workplace and ensure compliance with OSHA’s exposure limits.
The Role of Safety Officers in Preventing Lead Exposure
Safety officers play a critical role in managing occupational hazards associated with lead. Their responsibilities include:
- Conducting risk assessments
- Developing and implementing safety protocols
- Monitoring compliance with regulations
- Providing training and education to workers
By fostering a culture of safety and vigilance, safety officers help protect employees from the hidden dangers of lead.
Creating a Lead-Safe Workplace: A Case Study
Consider a construction company working on the renovation of a historic building. The project involves stripping old lead-based paint, which poses significant exposure risks to workers.
Step 1: Risk Assessment
The safety officer conducts a preliminary evaluation, identifying areas with lead-based materials.
Step 2: Implementing Controls
The company installs high-efficiency particulate air (HEPA) filtration systems to capture airborne lead particles and issues PPE to all workers.
Step 3: Ongoing Training
Employees attend a safety talk on lead exposure, where they learn about its health risks and preventive measures.
Step 4: Monitoring
Regular air quality tests and blood lead level checks ensure that exposure remains below permissible limits.
By taking these proactive steps, the company successfully completes the project without compromising worker safety.
Conclusion: Prioritizing Safety in Lead-Exposure Environments
Lead exposure is a preventable hazard that requires concerted efforts from employers, employees, and safety officers. By implementing effective safety measures, complying with regulatory standards, and fostering a culture of awareness, workplaces can protect their employees from the severe health risks associated with lead.
Safety isn’t just a regulatory requirement—it’s a commitment to the well-being of every worker. By prioritizing lead exposure prevention, companies can create healthier, more productive environments for their teams.
“Start Your Website Journey Today – Exclusive Hostinger Discounts!”

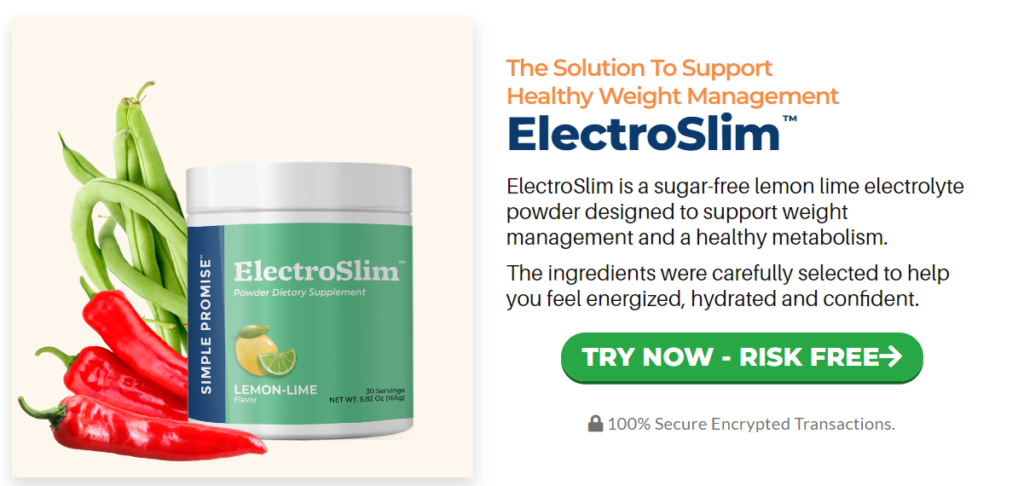

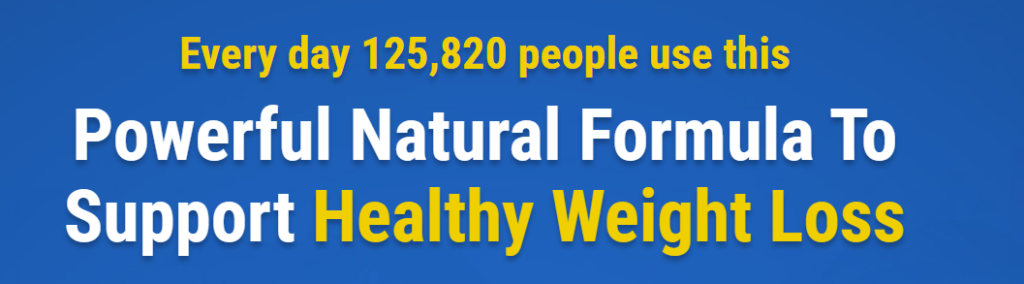

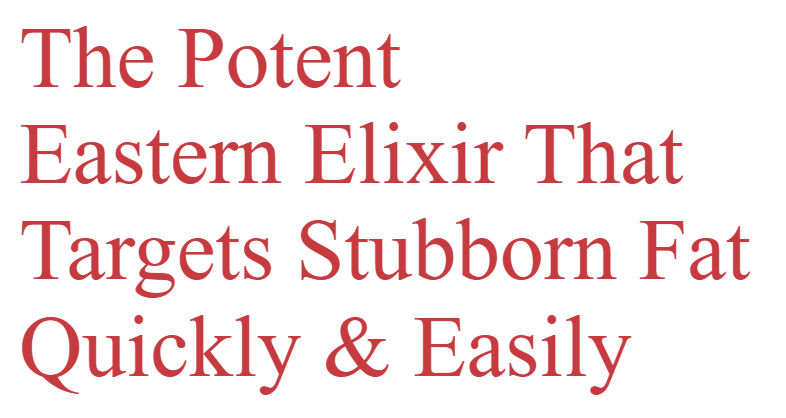
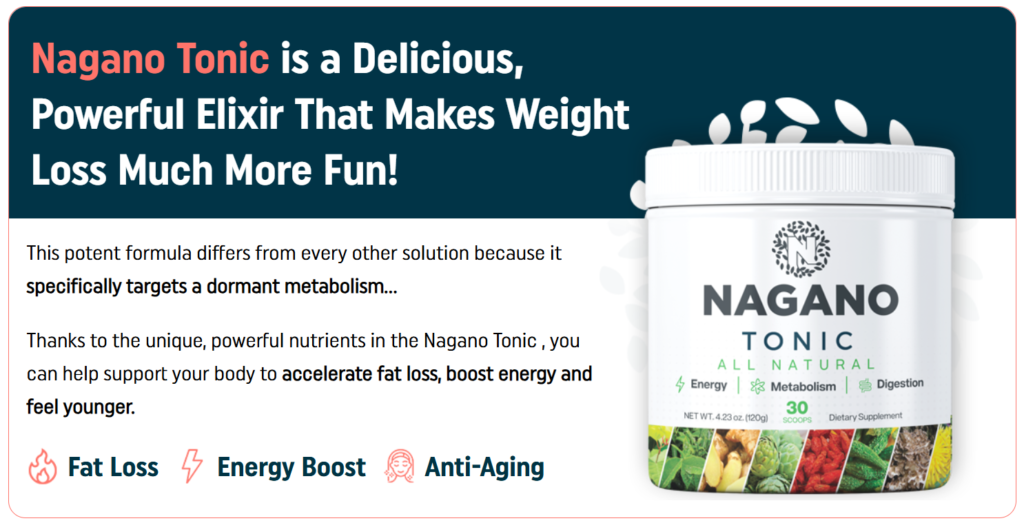