As a safety officer, ensuring proper rigging hardware practices is critical for preventing accidents and maintaining a safe work environment. Rigging hardware, including hooks, shackles, slings, and chains, plays an essential role in lifting and moving heavy loads. However, improper use, inspection, or maintenance of this equipment can lead to catastrophic failures, endangering workers and property. In this blog, we’ll cover key safety tips and best practices for rigging hardware to help you avoid potential hazards and ensure that your lifting operations are carried out safely and efficiently.
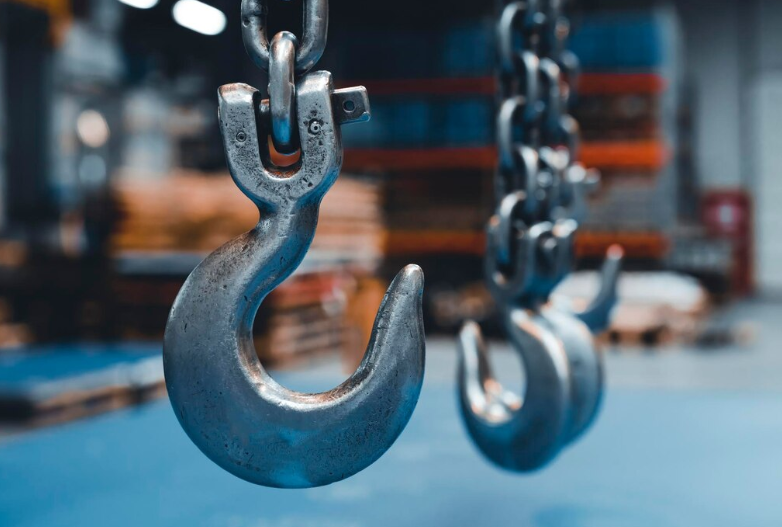
Safety Talk Points on Rigging Hardware:
1. Inspection Before Use – Always inspect rigging hardware, such as shackles, hooks, and slings, before each use for signs of wear, cracks, or damage.
2. Load Capacity – Know the rated load capacity of all rigging hardware and never exceed it. Overloading can lead to failure.
3. Proper Tagging – Ensure all hardware is properly tagged with the working load limit (WLL) and identification for traceability.
4. Compatibility – Use hardware that is compatible with the lifting equipment and rigging, including size, capacity, and type.
5. Manufacturer Guidelines – Follow the manufacturer’s instructions and guidelines for the use, care, and maintenance of rigging hardware.
6. Avoid Field Modifications – Do not modify or alter rigging hardware in the field. Only use it as designed and intended.
7. Correct Hook Usage – Hooks should be equipped with safety latches and never side-loaded. Ensure they are properly latched during use.
8. Shackle Pin Security – Ensure shackle pins are fully secured and that the load is applied correctly along the centerline to avoid bending or breakage.
9. Use of Slings – Inspect slings for fraying, wear, or damage. Never knot or twist slings during lifting operations.
10. Environmental Conditions – Be aware of environmental factors like moisture, heat, and cold, which can affect the strength and durability of rigging hardware.
11. Storage – Store rigging hardware properly when not in use to prevent rust, corrosion, and physical damage.
12. Rigging Angles – Monitor rigging angles, as extreme angles can significantly increase stress on the rigging hardware and lead to failure.
13. Proper Sling Attachment – Attach slings to lifting points without sharp edges that could cut or damage the hardware.
14. Avoid Shock Loading – Avoid sudden jerks or shock loading, which can cause rigging hardware to fail unexpectedly.
15. Certification and Training – Ensure workers handling rigging hardware are properly trained and certified in rigging safety.
16. Routine Maintenance – Schedule regular maintenance and lubrication of rigging hardware, especially moving parts like pulleys and sheaves.
17. Avoid Overhead Loads – Never stand or walk under a suspended load. Always ensure a clear and safe area beneath.
18. Locking Mechanisms – Verify that all locking mechanisms, such as locking pins or cotter pins, are securely in place before lifting operations begin.
19. Safe Lifting Practices – Plan lifts carefully, considering weight distribution, hardware placement, and coordination among the rigging team.
20. Emergency Procedures – Be aware of emergency procedures in case of rigging failure or accidents. Quick response can prevent injuries or fatalities.
“Start Your Website Journey Today – Exclusive Hostinger Discounts!”
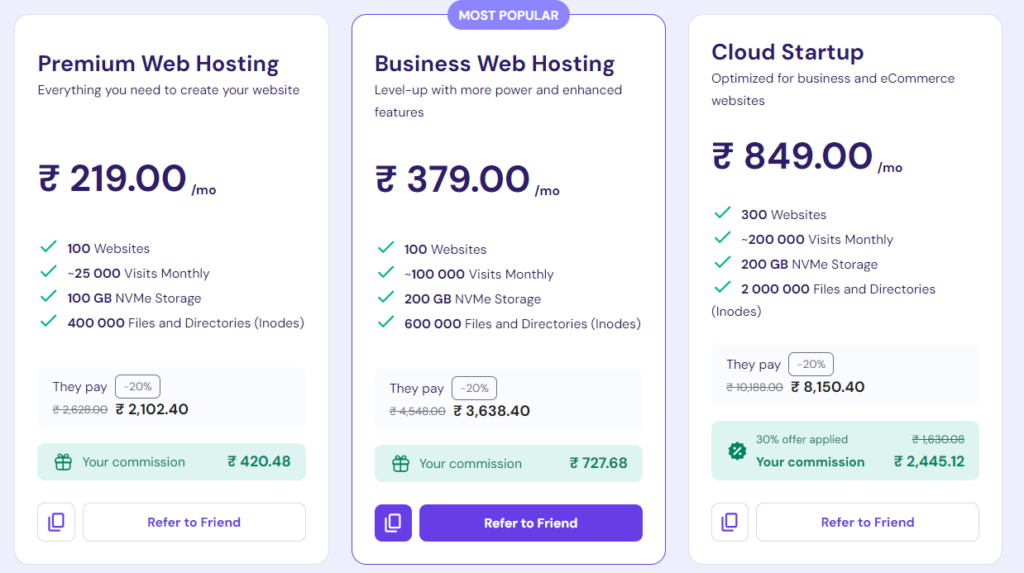
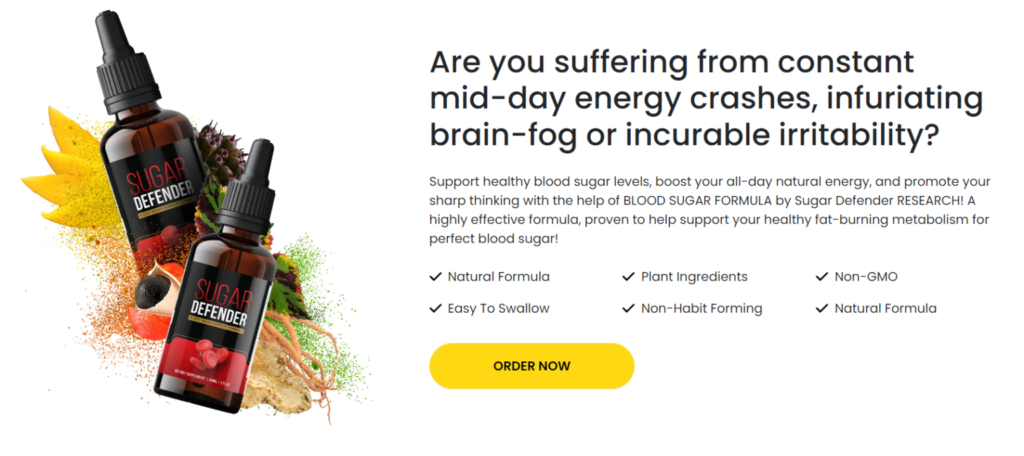
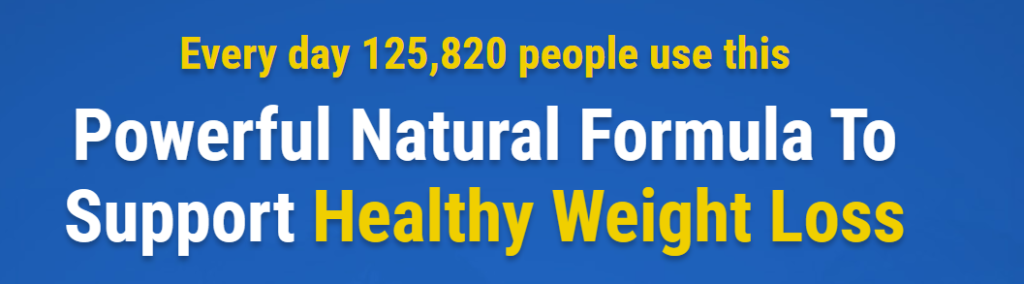